From Initial Ideas to CAD Drawings
The process of developing customised furniture begins with a spark of creativity. Our journey starts with initial ideas, which are often inspired by the client’s vision, needs, and the intended use of the furniture. During this stage, we focus on understanding the exact requirements, preferences, and expectations of our clients. We gather detailed information through consultations, sketches, and reference images. This collaborative effort ensures that the final product is a true reflection of the client’s desires.
Once we have a clear understanding of the concept, our skilled designers translate these initial ideas into CAD (Computer-Aided Design) drawings. CAD drawings are precise and detailed representations of the furniture, providing a comprehensive visual of the dimensions, shapes, and features. This stage is crucial as it allows for thorough examination and modifications before moving forward.
Transforming CAD Drawings into 3D Renderings
With the CAD drawings approved, the next step is to create 3D renderings. These renderings offer a realistic, three-dimensional view of the furniture, showcasing how it will look in its final form. Using advanced software, our designers add textures, colours, and materials to the renderings, making them as lifelike as possible.
3D renderings are invaluable as they provide clients with a tangible preview of the finished product. This step helps in identifying any potential design flaws and making necessary adjustments. It also allows clients to visualize the furniture in their space, ensuring it meets their aesthetic and functional requirements.
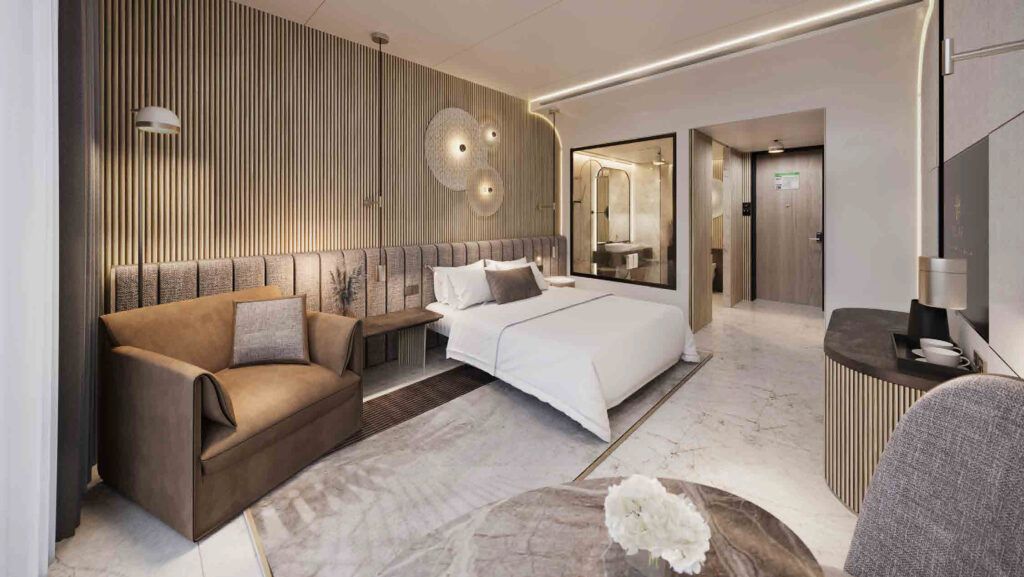
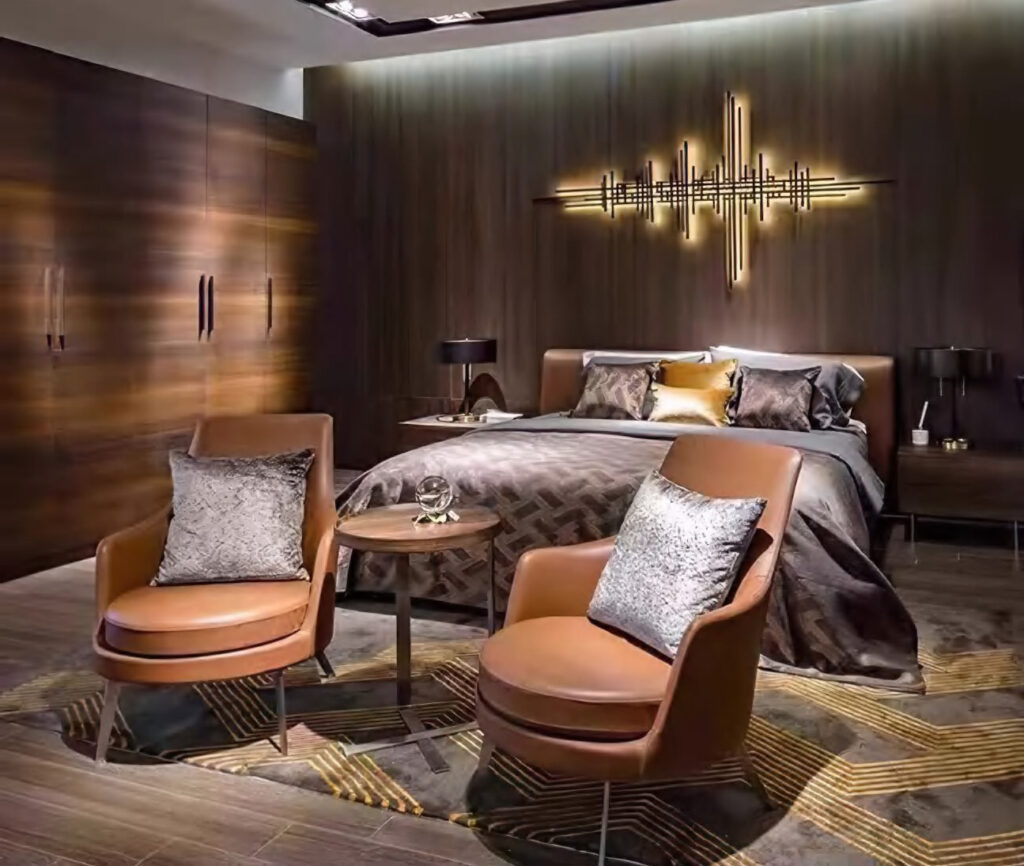
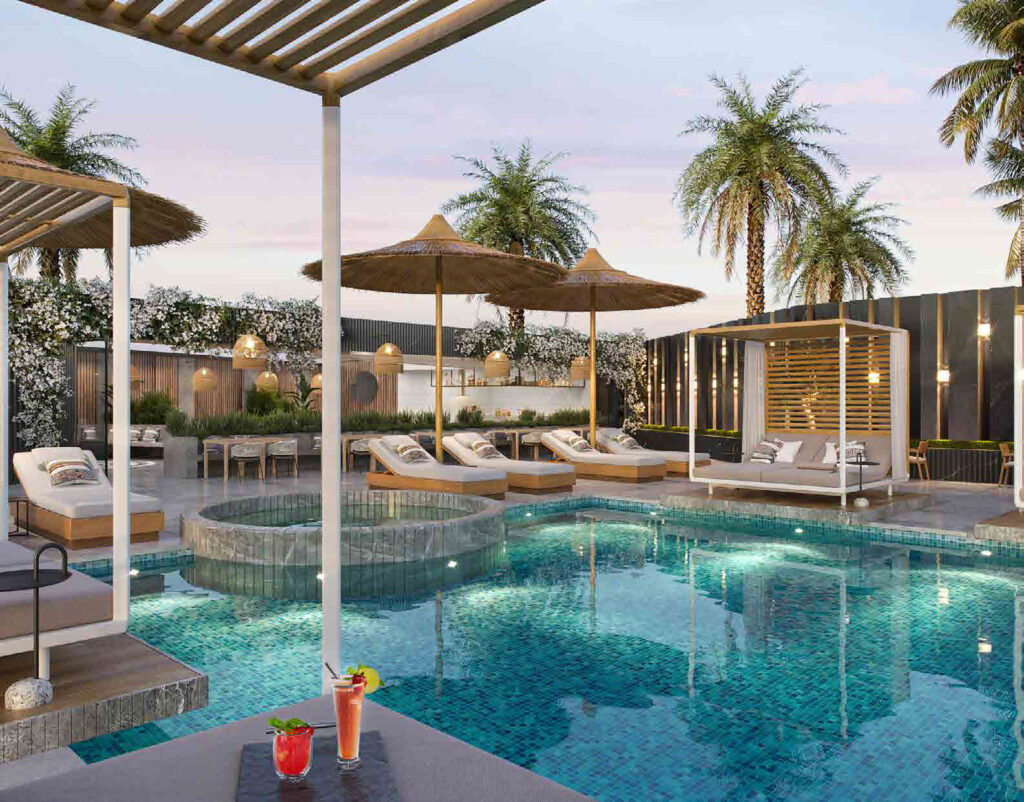
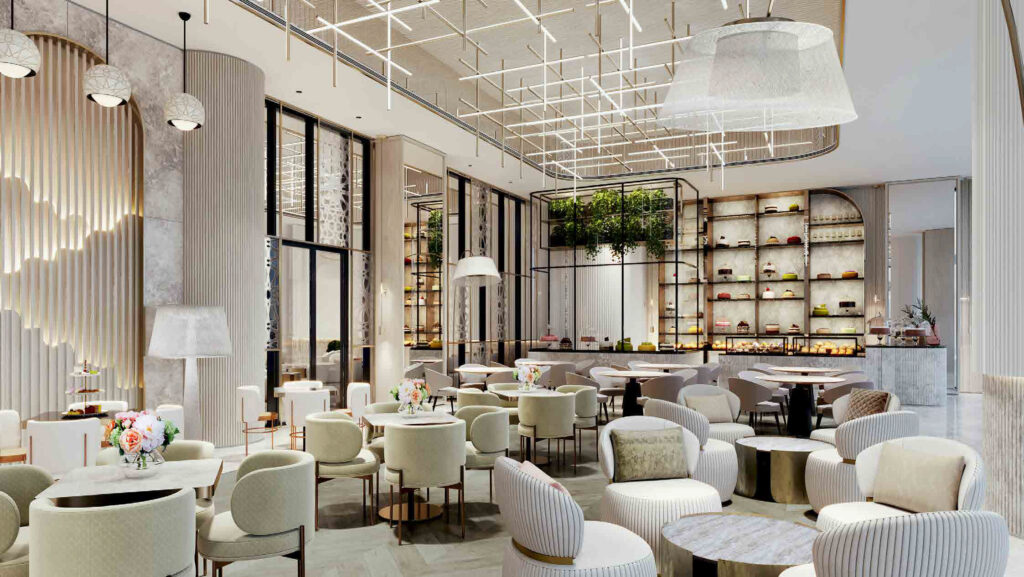
Client Approval and Refinements
Client satisfaction is paramount in the customised furniture development process. Once the 3D renderings are completed, we present them to the client for approval. This stage involves a thorough review of the design, dimensions, materials, and overall aesthetics. Any feedback or concerns raised by the client are addressed promptly, and refinements are made accordingly.
This collaborative approach ensures that the final design aligns perfectly with the client’s vision. The approval process is iterative, often involving multiple rounds of revisions until the client is completely satisfied with the design.
Creation of a Detailed Material Board
After the design is finalized, we move on to creating a material board. A material board is a curated collection of all the necessary materials required for the project. This includes wood types, fabrics, finishes, hardware, and any other components that will be used in the construction of the furniture.
The material board serves as a tactile representation of the design, allowing clients to see and feel the materials that will be used. It provides an opportunity to make final adjustments to material choices, ensuring that the selected materials align with the desired quality, durability, and aesthetics.
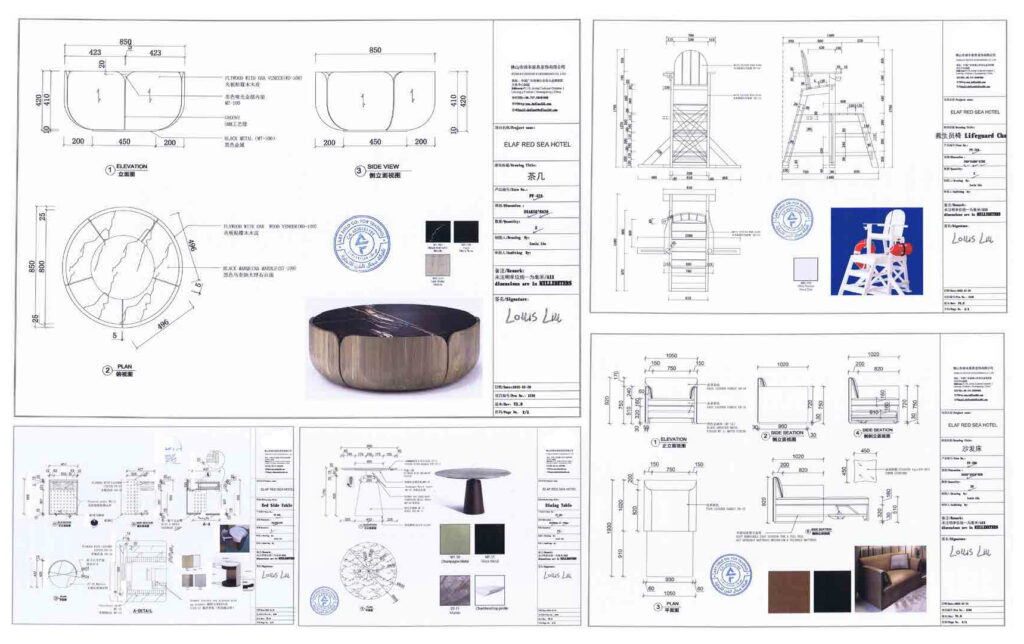
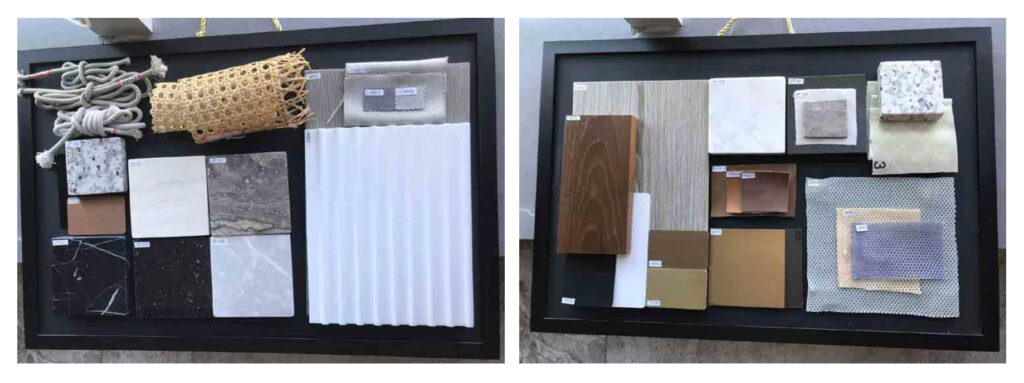
Developing a Delivery Schedule
With the design and materials finalized, the next step is to create a delivery schedule. This schedule outlines the timeline for the entire project, from sourcing materials to final delivery. It includes key milestones such as material procurement, manufacturing phases, quality inspections, and shipping dates.
A well-defined delivery schedule ensures that the project progresses smoothly and on time. It helps in coordinating with suppliers, managing resources, and setting realistic expectations for the client. Transparency in scheduling also allows clients to plan accordingly, especially if the furniture is intended for a specific event or space.
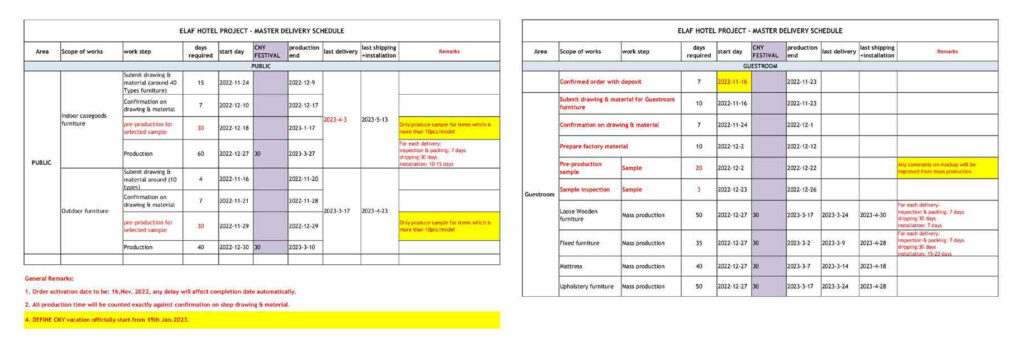
Manufacturing and Quality Inspections
The actual manufacturing of the customised furniture is where craftsmanship and precision come into play. Our skilled artisans and craftsmen bring the design to life using state-of-the-art machinery and traditional woodworking techniques. Each piece of furniture is meticulously crafted, paying attention to every detail to ensure superior quality and durability.
Quality inspections are an integral part of the manufacturing process. Throughout various stages of production, rigorous quality checks are conducted to ensure that the furniture meets the highest standards. These inspections cover aspects such as structural integrity, finish quality, and adherence to design specifications. Any defects or inconsistencies are addressed immediately to maintain the integrity of the final product.
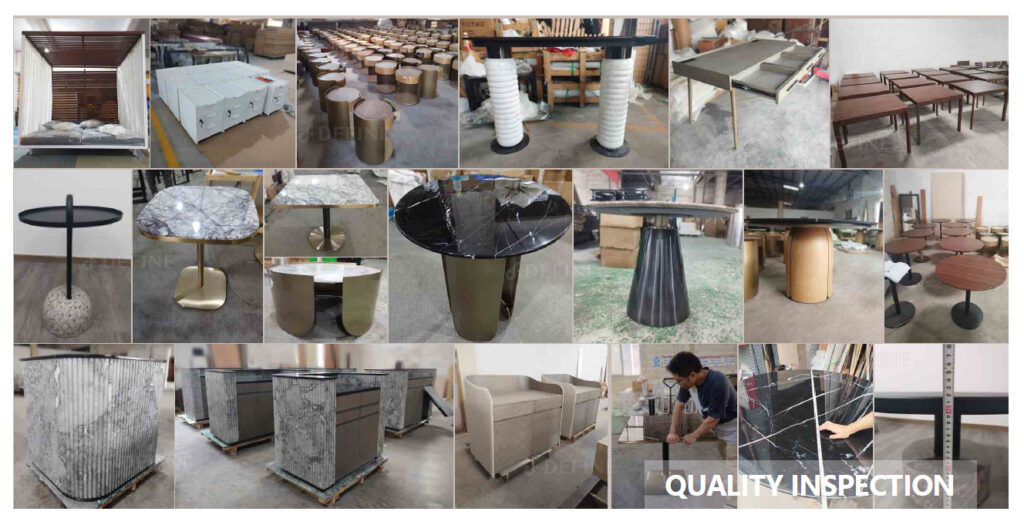
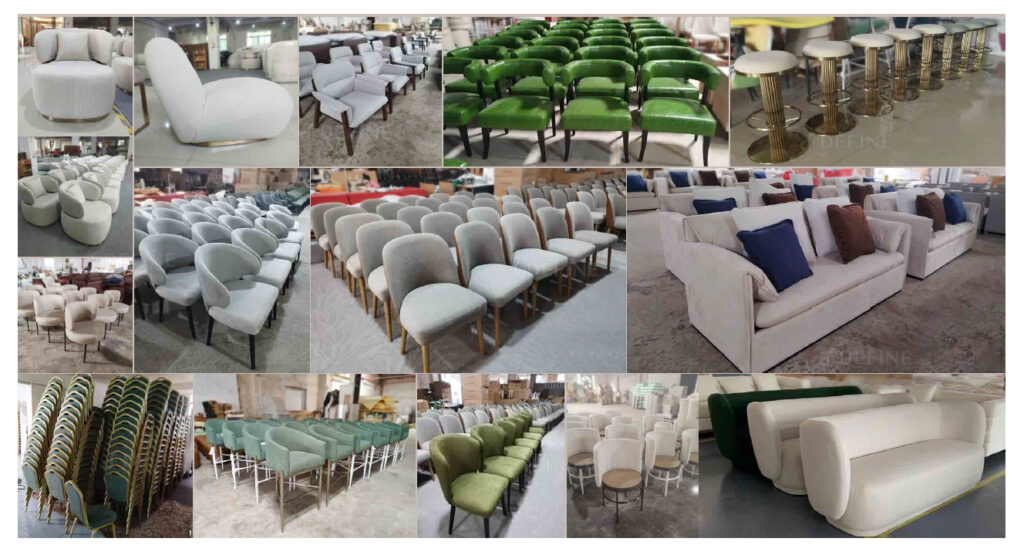
Final Quality Inspections Prior to Shipping
Before the furniture is shipped, a final round of quality inspections is conducted. This comprehensive check ensures that every aspect of the furniture meets the agreed-upon standards and specifications. The final inspection covers everything from structural stability to the finish, ensuring that the furniture is flawless and ready for delivery.
The final quality inspection is crucial as it guarantees that the client receives a product that is not only aesthetically pleasing but also durable and functional. It reflects our commitment to delivering high-quality customised furniture that exceeds client expectations.
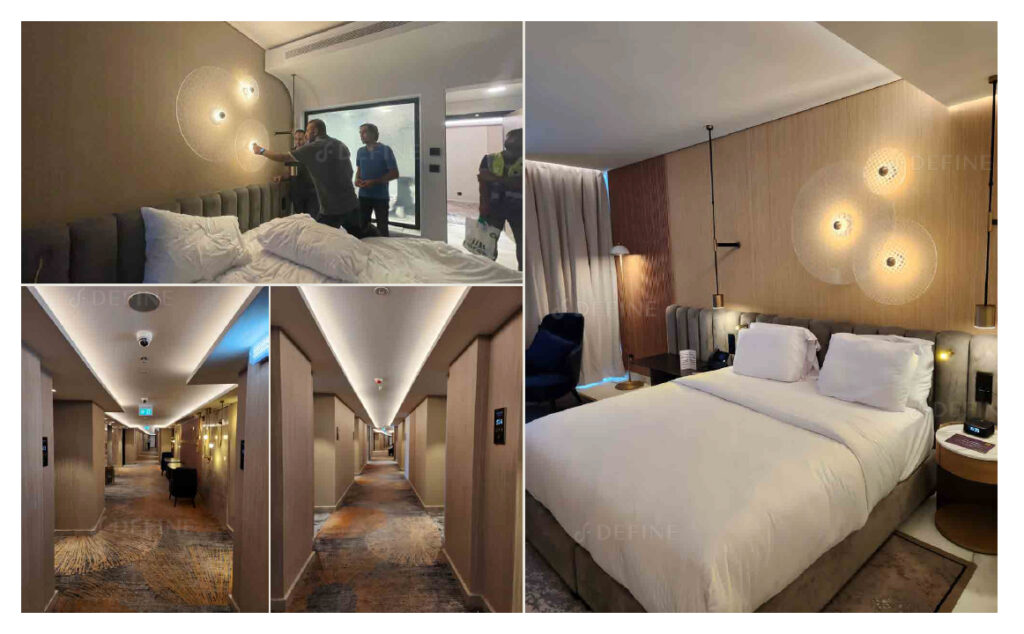
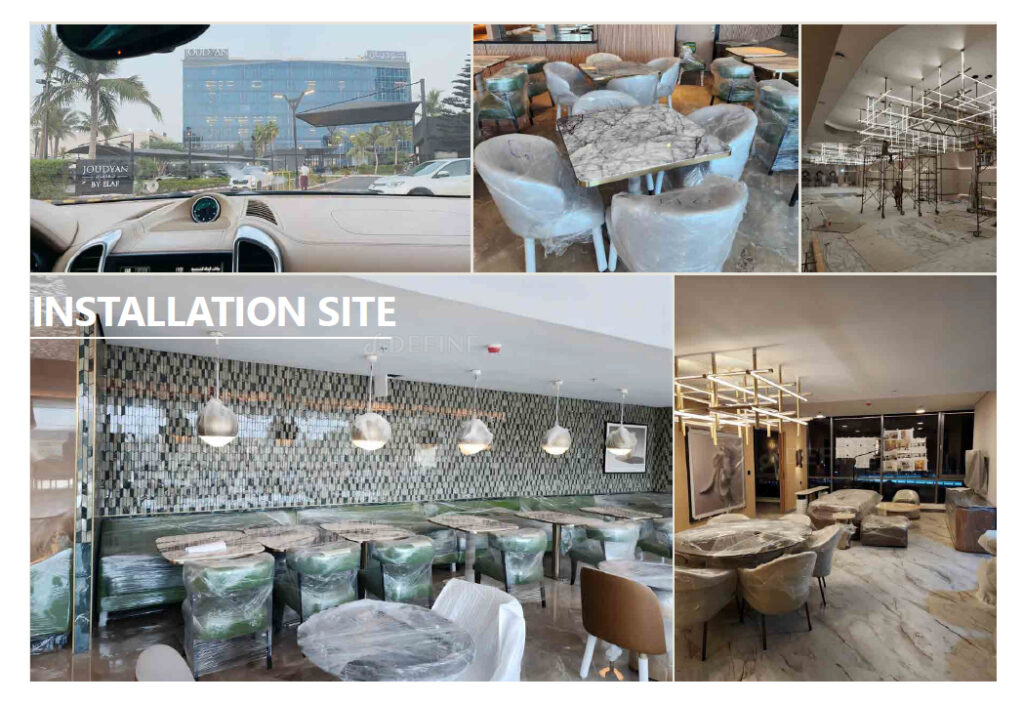
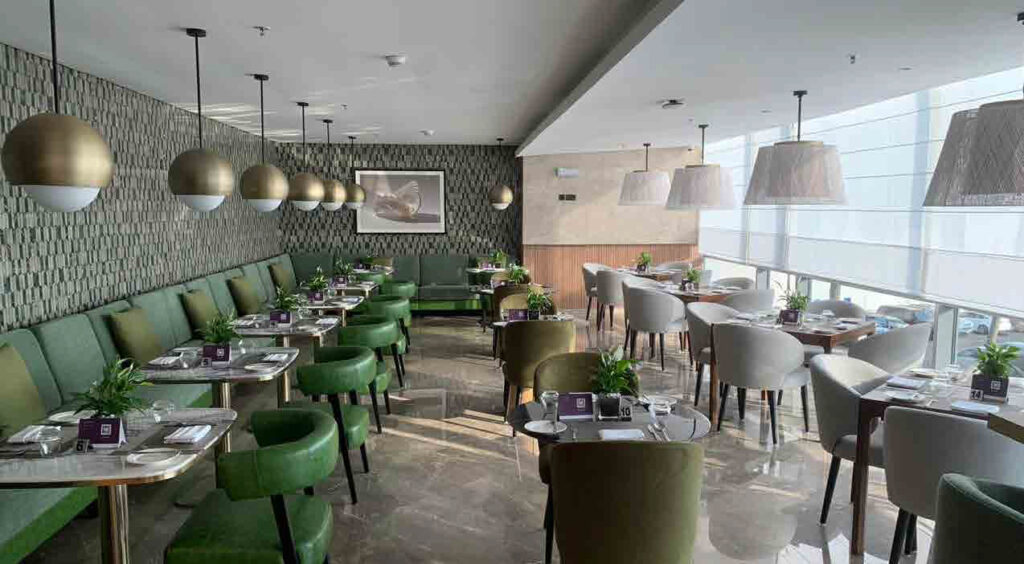
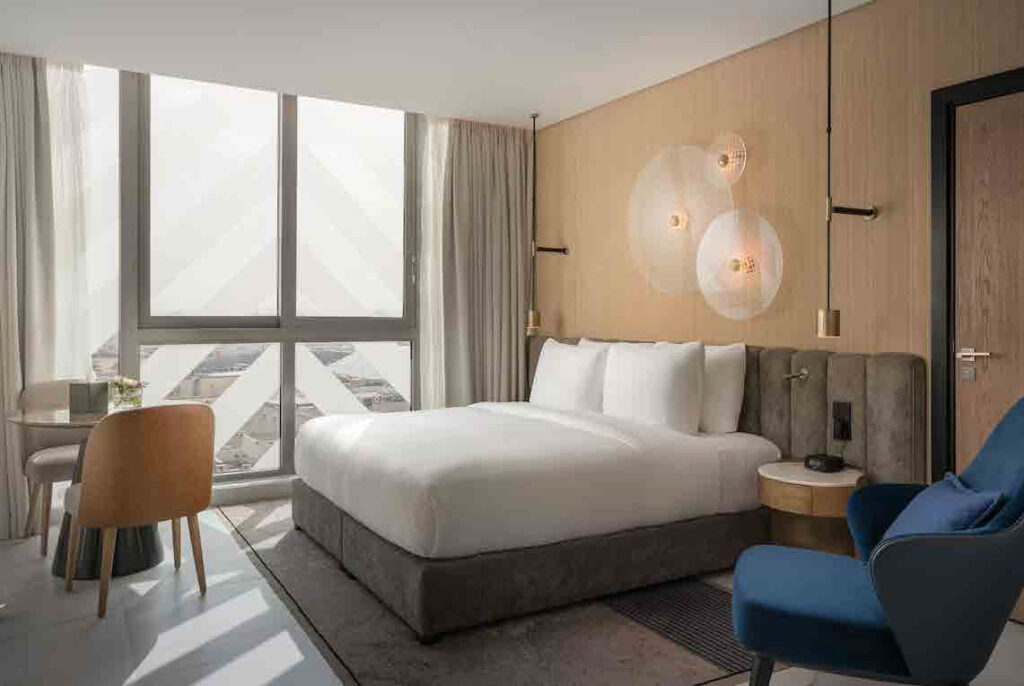
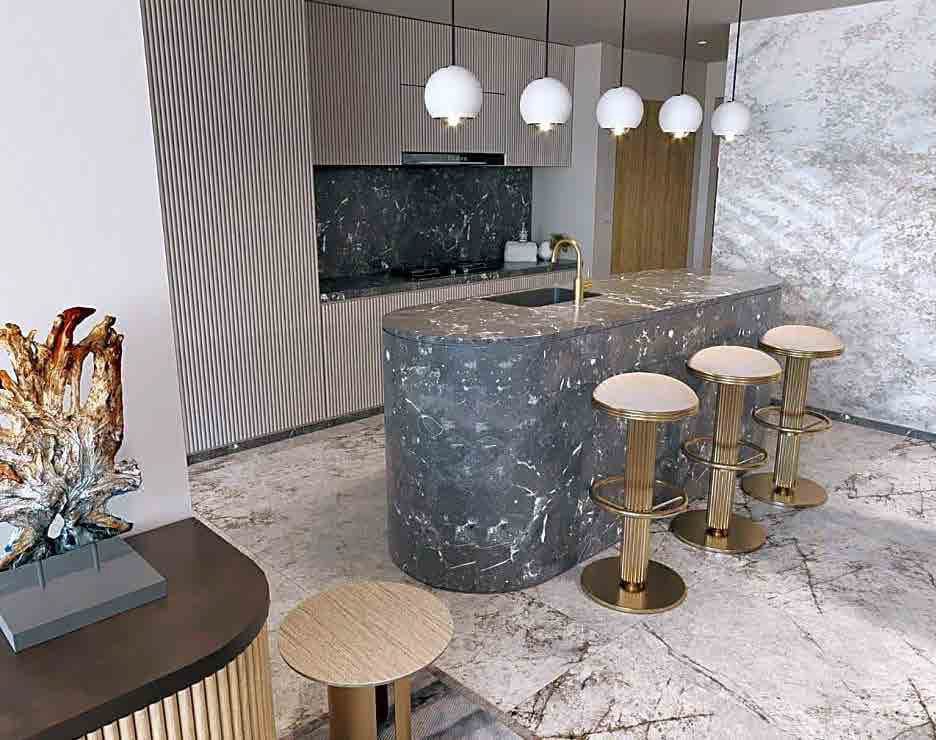
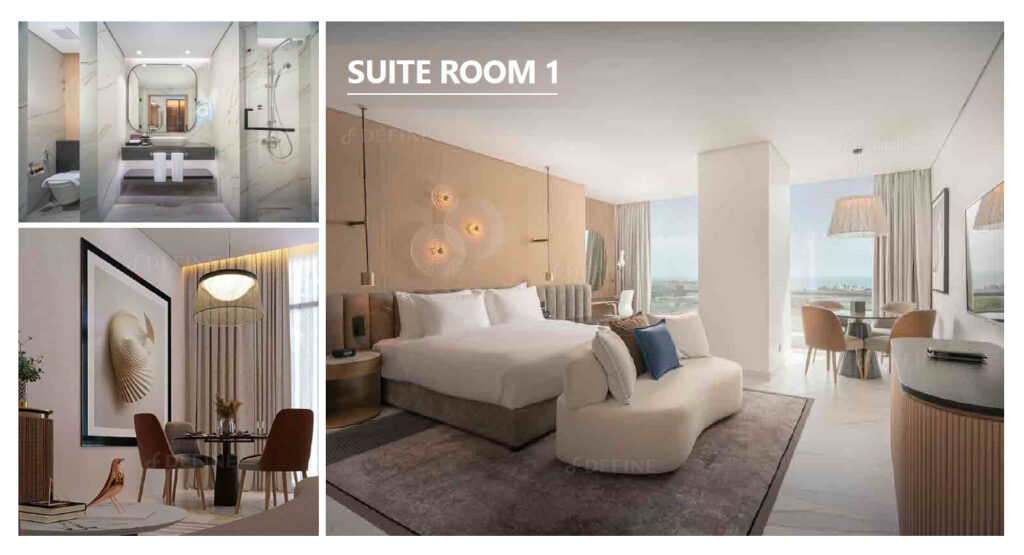
Conclusion: Delivering Excellence in Customised Furniture
The journey of developing customised furniture is a meticulous and collaborative process. From initial ideas to CAD drawings, 3D renderings, material selection, and quality inspections, every step is undertaken with precision and dedication. Our commitment to excellence ensures that the final product is a perfect blend of functionality, aesthetics, and craftsmanship.
By adhering to this comprehensive process, we deliver customised furniture that not only meets but exceeds client expectations. Our attention to detail and focus on quality make us a trusted partner in creating bespoke furniture solutions.